Western鈥檚 Pilot Plant gains machine to create recyclable, compostable trays
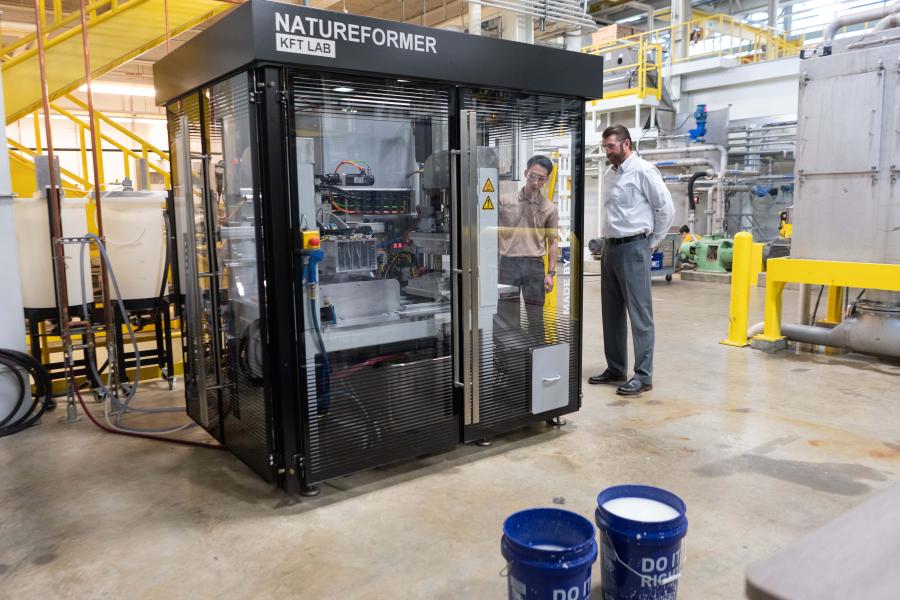
Doctoral student Jason Wang and Lon Pschigoda, WMU Pilot Plant general manager, work with the machine donated by Germany-based Keifel Technologies.
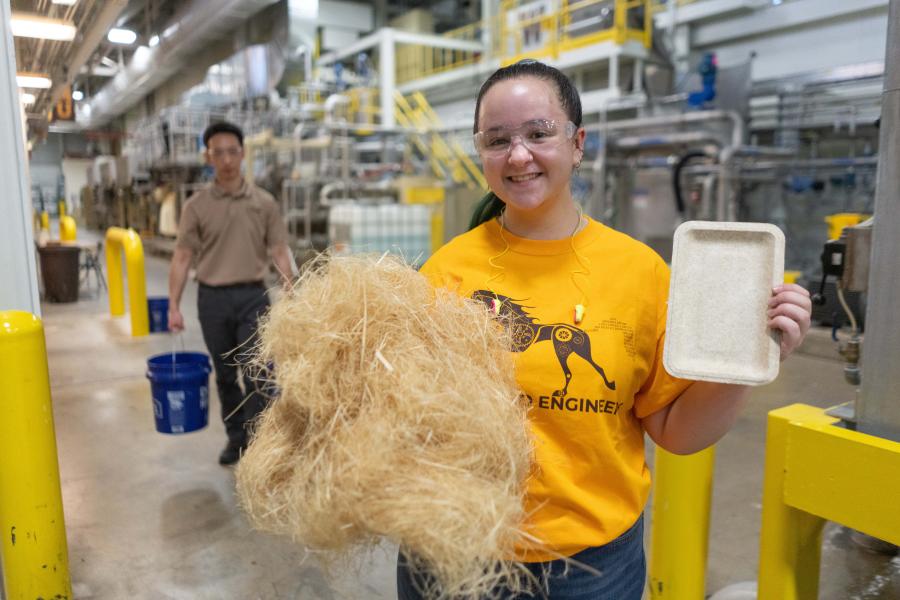
Senior Isabelle Ownby holds a tray made from recyclable and compostable materials.
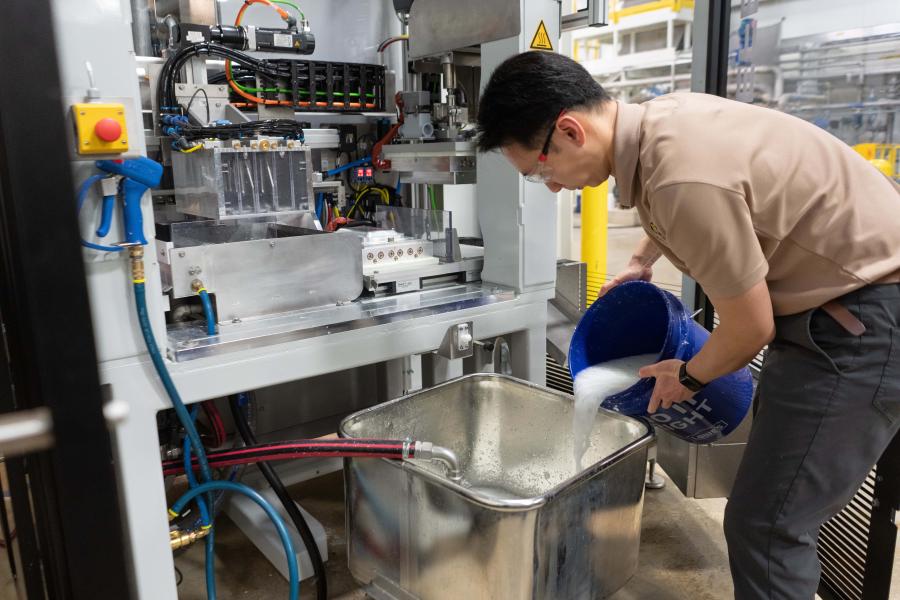
Wang pours a wet slurry that is 99% water and 1% fiber to make 3D food packing products at the WMU Pilot Plant.

WMU's Pilot Plant is able to create food packing products such as shallow and deeps trays.
KALAMAZOO, Mich.鈥擶estern 九一麻豆制片厂 University has partnered with Kiefel Technologies to become one of a select few institutions in the country that are utilizing technology to create 3D packaging products from recyclable and compostable fiber-based materials, reducing plastic usage and waste.
The machine currently produces two molded-fiber shapes鈥攁 shallow tray and a deep tray鈥攚ith plans to expand to a cup in the future, says Lon Pschigoda, general manager of the WMU Pilot Plant.
鈥淢olded fiber is growing in popularity due to consumer demand, brand awareness and anti-plastic legislation,鈥 he says. 鈥淭he shapes and sizes that can be formed and used are almost endless. This is a very exciting space for innovation and research.鈥
鈥淚t鈥檚 a good fit for us,鈥 he adds of the equipment. 鈥淲e already have traditional papermaking equipment, along with pulping and fiber development capability, as well as recyclability and composability certification testing. The WMU Pilot Plant is known for our excellent staff and facilities, working on the cutting edge of all things pulp and paper, especially food service packaging.鈥
The process uses a wet fiber slurry that is 99% water and 1% fiber, Pschigoda explains. The fiber slurry is pulled into a forming screen with vacuum, then transferred to a station where the moisture is pressed out and finally transferred to a heated press, leaving the molded form to dry. Pulp goes in and a ready-to-use fiber tray comes out. The fully automated process is awesome to see, he says.
Curbing consumer waste and reducing its effects on the environment has fueled consumer demand and, in some cases, legislative requirements for sustainable products, he adds.
鈥淓specially in food service applications, where lifespan is short and the product is a vehicle for food waste, it makes so much sense to move away from plastic wherever possible to a compostable or recyclable fiber option.
鈥淥ver the next five to 10 years, packaging producers are going to be buying machines faster than they can build them,鈥 he says.
The state-of-the-art technology was donated by Germany-based Keifel Technologies and installed in the fall, with the only other machines of this kind in the U.S. available at the University of Washington and University of Maine. WMU will offer this machine to industries and allow for clients to come onsite and perform their research and development efforts. Current research efforts include the use of alternative fibers鈥攈emp, wheat straw, agricultural waste鈥攁nd adding barrier properties鈥攚ater resistance, grease resistance, oxygen barrier鈥攖o molded fiber products.
鈥淜iefel is a leading manufacturer of natural fiber-forming equipment. Teaming up with WMU allows both sides to further develop and expand the use of natural fiber for important applications in the packaging industry. It also helps to expose the next generation of passionate people to the industry via research and coop opportunities,鈥 says Matt Sieverding, president and CEO of Kiefel parent company Brueckner Group USA.